Are you looking for water-based adhesives manufactured according to your needs or specifications? Water-based adhesives are manufactured by combining water, polymers and additives. The adhesives are typically activated as the water evaporates or is absorbed by the substrate. Matco develops and manufactures a wide range of water-based adhesives for different types of end customers and applications. We produce water-based adhesives based on synthetic and natural polymers:
Water-based adhesives based on synthetic polymers
- Adhesives Based on Homo-polymer Emulsions:
- Chemical Composition: These adhesives are composed of a single type of polymer, such as polyvinyl acetate (PVA) or another specific homo-polymer.
- Bonding Strength: They generally offer good bonding strength, especially on porous materials like paper, cardboard, and wood.
- Drying Time: Homo-polymer emulsion adhesives typically have a relatively fast drying time, which can vary depending on the specific formulation and environmental conditions.
- Flexibility: The flexibility of these adhesives can be adjusted based on the choice of polymer. They are often suitable for applications that require some degree of flexibility.
- Water Resistance: Their water resistance can vary, but they may not perform well in fully immersed or highly humid conditions.
- These properties can be fine-tuned through formulation and additives to meet the specific requirements of different applications, making water-based adhesives suitable for a wide range of industries and purposes.
- Adhesives Based on Copolymer Emulsions:
- Chemical Composition: Copolymer emulsion adhesives are made from a mixture of two or more different polymers, creating a copolymer with a combination of their properties.
- Versatility: These adhesives are versatile and can be tailored to have a wide range of properties, including variations in bonding strength, flexibility, and water resistance.
- Bonding to Different Substrates: Copolymer emulsion adhesives are often designed to adhere well to various substrates, including both porous and non-porous surfaces.
- Drying Time: Their drying time can be adjusted to suit specific applications, providing flexibility in assembly processes.
- Water Resistance: Depending on the formulation, copolymer emulsion adhesives can offer improved water resistance compared to homo-polymer emulsions.
- Adhesives Based on Acrylates:
- Chemical Composition: Acrylic water-based adhesives are based on acrylate polymers.
- Bonding Strength: They provide excellent bonding strength, often superior to many other water-based adhesive types, and can bond to a wide range of substrates, including plastics, metals, and composites.
- Durability: Acrylic water-based adhesives are known for their durability and resistance to environmental factors, including UV radiation and temperature extremes.
- Flexibility: They can be formulated to have various levels of flexibility, making them suitable for both rigid and flexible applications.
- Drying Time: Many acrylic water-based adhesives offer rapid curing, which is advantageous in high-speed production environments.
- Adhesives Based on Synthetic Latex:
- Chemical Composition: These adhesives are water-based and contain polymer particles created through emulsion polymerization. They can be based on various synthetic materials, such as styrene-butadiene rubber (SBR), acrylics, or vinyl acetate.
- Versatility: Synthetic latex water-based adhesives can be versatile, with properties customized for specific applications. They are commonly used in woodworking, paper bonding, textiles, and more.
- Bonding Strength: They offer good bonding strength, especially on porous materials.
- Water Resistance: Their water resistance can vary, but they are generally more resistant to moisture compared to some other water-based adhesives.
Water based adhesives based on natural polymers
- Chemical Composition:
- Natural Origin: These adhesives are derived from natural sources, primarily the latex sap obtained from rubber trees (Hevea brasiliensis).
- Polymerization: Natural latex contains mainly cis-1,4-polyisoprene as the polymer. It also contains proteins, carbohydrates, and water.
- Bonding Strength:
- Good Adhesion: Latex adhesives provide good adhesion, especially on porous materials such as paper, cardboard, textiles, and wood.
- Less Suitable for Non-Porous Substrates: They may not bond as effectively to non-porous surfaces like plastics and metals compared to other adhesive types.
- Drying Time:
- Moderate Drying Time: Latex adhesives typically have a moderate drying time. The water content in the adhesive needs to evaporate for the bond to set.
- Pressure-Sensitive: They may exhibit pressure-sensitive properties during the drying phase, requiring pressure for proper adhesion.
- Flexibility:
- Elasticity: Latex adhesives are known for their flexibility and elasticity. They can accommodate some degree of movement and expansion in bonded materials without losing adhesion.
- Ideal for Flexible Materials: They are often used for applications involving flexible substrates or materials that experience dimensional changes.
- Water Resistance:
- Moderate Water Resistance: While latex adhesives can resist mild moisture exposure, they are not entirely waterproof. Prolonged immersion or exposure to water can weaken the bond.
- Environmental Considerations:
- Eco-Friendly: Latex adhesives are generally considered more environmentally friendly than some synthetic counterparts because they are derived from renewable resources.
- Low VOCs: They typically have low volatile organic compound (VOC) emissions, making them suitable for indoor applications where air quality is a concern.
Applications of water-based adhesives
- (Spiral) Ducts and Angle Profiles:
- Water-based adhesives are used in the HVAC (heating, ventilation, and air conditioning) industry to bond and seal (spiral) ducts and angle profiles. These adhesives provide a strong and durable bond for joining metal components in air duct systems.
- Laminating:
- Water-based adhesives are widely used for laminating processes in industries such as packaging, graphics, and woodworking. They are applied between layers of materials like paper, cardboard, film, or wood to create laminated structures with enhanced strength and durability.
- Closing of Boxes:
- In packaging and shipping, water-based adhesives are employed for sealing corrugated boxes, ensuring that they remain securely closed during transportation and storage. They are commonly used in the packaging of various goods for shipping.
- Production of Displays:
- Water-based adhesives play a crucial role in the production of displays, such as point-of-purchase displays (POP displays) and signage. These adhesives help assemble the components and graphics that make up these promotional materials.
- Honeycomb:
- Water-based adhesives are used in the production of honeycomb structures, which are lightweight yet strong structures often used in aerospace, automotive, and construction applications. These adhesives help bond the layers of material that form the honeycomb structure.
- Bookbinding:
- Bookbinding relies on water-based adhesives for binding the pages of books, magazines, and catalogs. These adhesives provide a secure and long-lasting bond while allowing the pages to flex open without damage.
- Insulation:
- In the construction industry, water-based adhesives are used to bond insulation materials such as foam boards, fiberglass, or mineral wool to walls, ceilings, and other building surfaces. They help improve energy efficiency by creating a continuous thermal barrier.
- Labels and Envelopes:
- Water-based adhesives are applied to labels, allowing them to adhere to various surfaces, including packaging, products, and documents. They are also used in envelope manufacturing for sealing purposes, ensuring that envelopes remain closed during transit.
Water-based adhesives are valued for their versatility and environmentally friendly characteristics, making them suitable for a wide range of applications in different industries. They are often preferred for their low volatile organic compound (VOC) emissions and ease of clean-up, making them a more sustainable choice compared to some solvent-based adhesives.
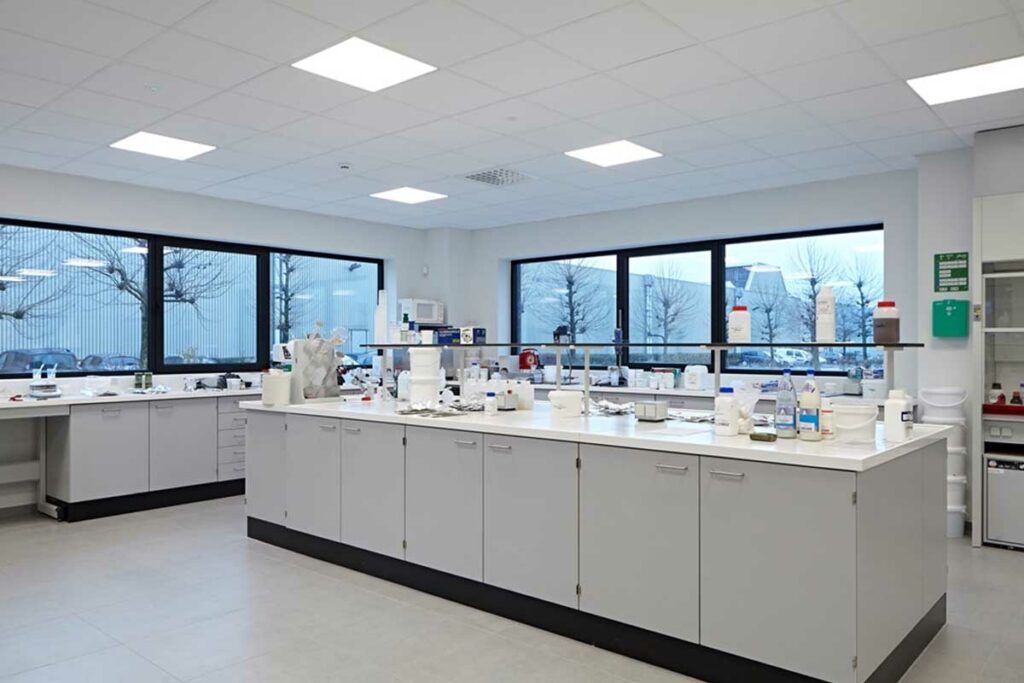
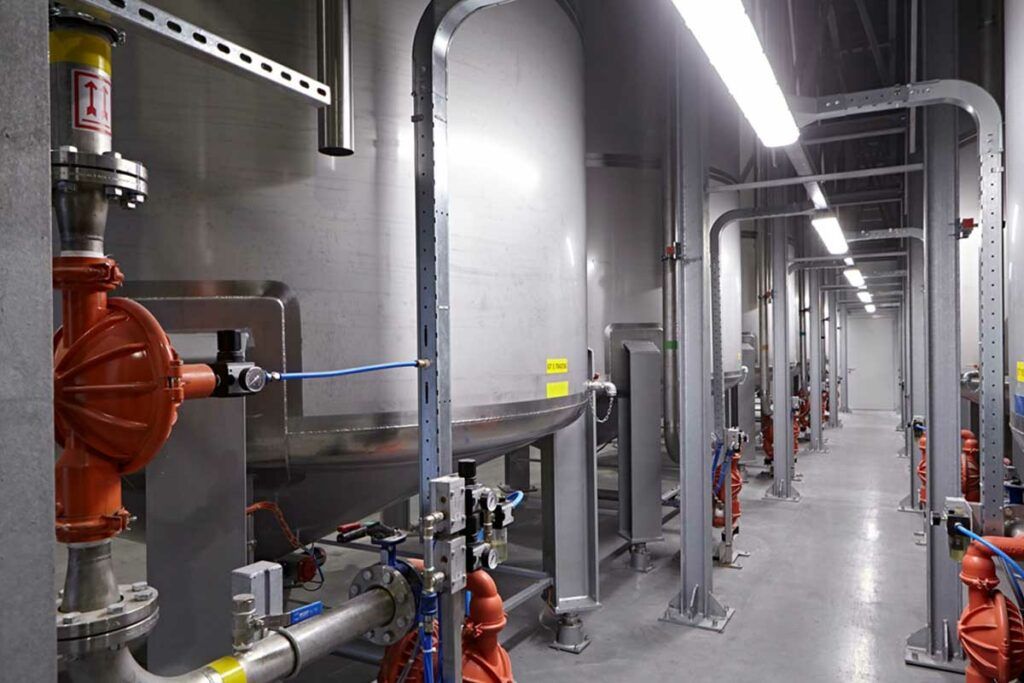
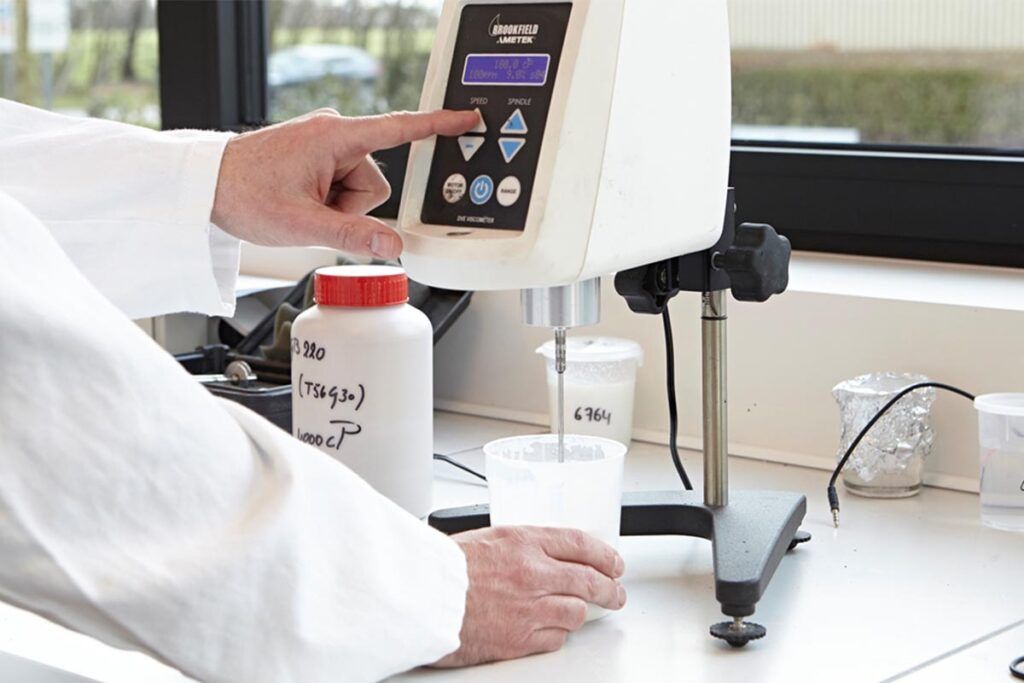